Revitalization — "bringing back to life"
The word revitalization (latin. vita — life) can be literlly interpreted as "bringing back to life". The discovery of the revitalization phenomenon is based on the unique physical and chemical processes as a result of friction which occurs under specific conditions.
In brief, the essence of the phenomenon is as follows: when a mechanism is operating, stress is formed on the friction surfaces. Under high load excessive thermal energy is released destroying and wearing parts.
However, if a unique building material — revitalizant is introduced to the friction area, it converts the excessive energy to form a new coating. Therefore from friction's destructive energy positive conditions are formed. The energy of destructions turns into the energy of creation!
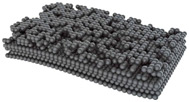
Wear and tear of the operating surface
In order for a defect to occur it is enough to have a scratch or a chip emerged due to impact of solid foreign particles (dust, dirt or cutting waste). This area becomes a zone of enormous surface activity. It appears in places where metal atoms have uncompensated connections. So they can be easily “loosened” and torn from the matrix when the load increases. Metal starts chipping.
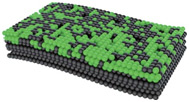
Start of the revitalization process
The revitalizant gets onto the operating surface together with the lubricant. The revitalizant starts acting exactly in the zone of the heaviest wear, as there is enough excess energy here to start to start the revitalization process, and metal atoms possess the largest number of uncompensated connections. These connections, like magnets, capture and hold the building material, revitalizant, just in the areas of wear and tear.
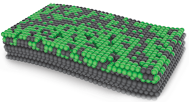
New coating formation
In a few minutes after beginning of the revitalization process a ceramic-metal patch appears in the place where a scratch was. The zone of enormous activity disappears. The energy processes stabilize, the growth of the ceramic-metal coating stops.
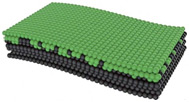
Completion of the surface modification
Due to diffusion of the protective layer into metal an extremely firm gradient ceramic-metal coating with unique operating properties is created.
Revitalization results
The potential of revitalization has changed the modern conception of vehicle and machinery operation and repair. XADO products have created a hightech and yet very simple method to reverse the wear.
As a result of revitalization a new coating is formed on the surface of the friction pairs — a part builds up and restores its geometry. The new coating possesses unique properties: an amazing durability (microhardness 650–750 kg/mm2), high corrosion resistance, and a very smooth surface (Ra up to 0.06 micron). That is why a part is guaranteed to last by up to 2–4 times longer after the revitalization. The revitalized mechanism will also be indebted to you and will continue to operate at its best!
The benefit of the revitalization is that you will end up with a mechanical assembly which will perform better than new and which will last longer than it would have done!
Benefits of revitalization
Repair and Restoration of Assemblies. New metalloceramics coating is formed on the friction pairs; these parts increase in weight and volume, and restore their initial geometry (the biggest increase is up to 1.5 mm!). The restoration occurs during normal mechanical operation so that the ideal fit of the friction pairs is achieved. As a result, the capacity of power units increase, the accuracy of the mechanism work improves, and noise and vibration are reduced.
Resources saving, significant reduction in the amount of assembly wear and tear. After revitalization the new coating possesses unique properties: amazing durability (micro-hardness 650–750 kg/mm2) and high corrosion resistance. It helps to prevent from further metal loss, to maintain an ideal friction surface and significantly increase the reliability of the assembly, to prolong their life span.
Power and energy saving. Another advantage of the metalloceramics coating is an abnormally low friction factor (roughness Ra up to 0.06micron). After treating the friction surfaces, it results in a significant increase (up to 30%) in energy saving.
Ecological rationality. The saving of energy and resources is the basic for environment protection. When a revitalized mechanism is operating, there is a significant reduction in the release of harmful exhaust substances (CO, CH, and NOx) to the atmosphere.
Demonstrably about the revitalization process
application
of revitalizant
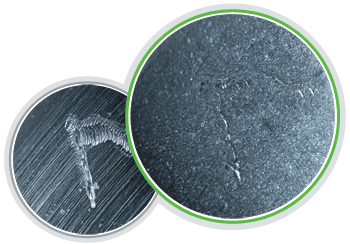
AFTER
application
of revitalizant
A real surface of a part before
and after the revitalization.